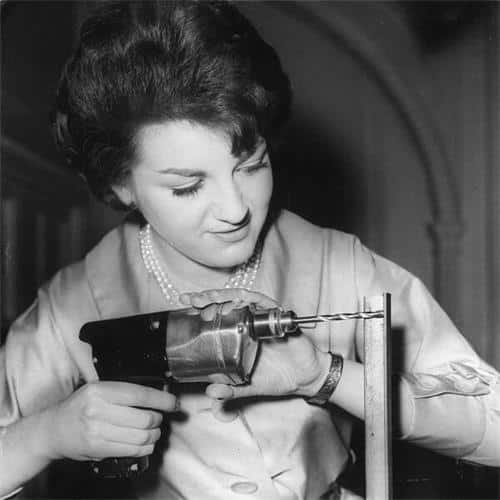
was being demonstrated in this photo from 1961.
Power tools have become an essential part of many people’s lives, whether it’s for professional or personal use. One of the most common power tools is the drill, which is used to make holes in various materials such as wood, metal, and concrete.
The drill has several components that work together to perform its function, including the power tool switch. The power tool switch is a crucial component of any drill because it controls the flow of electricity from the power source to the motor. It allows users to turn on and off their drills with ease and provides a level of safety by preventing accidental operation.
Understanding how power tool switches work in a drill can help users operate their equipment safely and troubleshoot issues if they arise. This article will explore how power tool switches work in a drill and provide insight into common issues and troubleshooting techniques for these essential components.
Introduction to Drill Switch
The power tool switch in a drill is a crucial component that allows for the control and operation of the tool.
It is important to understand the function and mechanism of these switches, as they can impact both safety and efficiency in their use.
In order to comprehend the role of power tool switches, it is helpful to have a basic understanding of how power tools operate and are constructed.
The importance of power tool switches in drills
Significance lies in the functionality of power tool switches within drills. These switches serve as the main control mechanism for the drill’s operation, allowing users to adjust torque and speed settings according to their specific needs.
The switch is responsible for regulating the flow of electricity from the battery or power source to the motor of the drill, thus controlling the speed and power output.
Power tool switches also play a crucial role in ensuring safety while using drills. With different settings for torque and clutch, users can avoid damaging screws or materials during drilling.
Additionally, reverse switch allows users to extract stuck screws or change bits easily without any hassle.
Power tool switches are important because they allow users to have more control over their drilling tasks, making it easier and safer to use these powerful tools in a variety of situations.
How power tools work
Understanding the mechanics behind handheld power tools is essential for ensuring their safe and effective use, with over 400,000 emergency room visits in the United States alone resulting from power tool accidents each year.
Power tools are designed to perform various tasks with a high level of efficiency and accuracy while minimizing physical strain on the user. To achieve these objectives, power tools utilize an electric motor that converts electrical energy into mechanical energy, which drives a range of functional components such as blades or drill bits.
One critical component in power tools is the switch assembly that controls the flow of electricity to the motor. The switch installation in drills, for example, enables users to turn on or off their devices by merely pressing a button or flipping a lever. Depending on its design and purpose, a switch can also regulate speed levels or activate safety features such as automatic shut-off mechanisms in case of overloading or overheating.
Although seemingly insignificant compared to other parts like motors and batteries, power tool switches play an integral role in ensuring optimal control and user safety during operation.
Basics of Power Tools
Power tools are devices that use electricity, compressed air, or a gasoline engine to perform specific tasks for construction, manufacturing, and home improvement.
The purpose of power tools is to make work more efficient and less time-consuming than traditional hand tools. Some common types of power tools include drills, saws, sanders, grinders, and nail guns.
Definition and purpose of power tools
One fundamental aspect of power tools is their ability to provide efficient and effective means of completing tasks through the use of mechanical energy.
Power tools are defined as any tool that operates using a source of power, such as electricity or compressed air, rather than manual labor.
The purpose of power tools is to improve productivity by reducing the time and effort required to complete a task.
Manufacturers play a crucial role in producing high-quality power tools that meet industry standards and safety regulations.
These manufacturers go through rigorous testing processes before releasing their products into the market.
Additionally, suppliers and vendors help distribute these products to consumers worldwide.
One important component in power tools is the switch, which allows users to turn on or off the device with ease.
Overall, power tools have revolutionized various industries, including construction and manufacturing by providing fast and efficient solutions for complex tasks like drilling holes using drills with reliable switches manufactured by trusted factories.
Common types of power tools
In the previous subtopic, we discussed the definition and purpose of power tools. Now, let us delve deeper into the different types of power tools that are commonly used in various industries.
One of the most popular power tools is a drill, which has become an indispensable tool for both DIY enthusiasts and professionals.
There are two main types of drills: cordless drills and corded drills. Cordless drills are powered by rechargeable batteries and offer more flexibility as they can be used without being tethered to a power outlet. On the other hand, corded drills rely on a constant supply of electricity to operate.
Rotary drills are another type of drill commonly used for drilling through tough materials such as concrete or masonry. Regardless of their type, all these drills have one common component that is essential in their operation – the power tool switch assembly.
In our next subtopic, we will explore how this switch assembly works within a drill to control its speed and torque output during use.
Understanding the Components of a Drill
The third section of this article delves into the understanding of the various components that are integral to a drill’s functionality. These parts include the motor, chuck, battery (if applicable), and others.
A comprehensive explanation of each component will be given in an objective and impersonal tone, providing readers with a clear understanding of their roles within a drill.
The different parts that make up a drill (Motor, chuck, battery if applicable, etc.)
Comprised of a motor, chuck, and potentially a battery, the drill serves as a versatile and essential tool in many industries. The motor is the main component of the drill that provides it with power to operate. It is typically located at the base of the drill and can be either corded or battery-powered.
The chuck holds the drill bits in place and allows them to rotate freely while drilling into materials. There are various types of chucks available, including keyless chucks that allow for quick bit changes without needing a special tool.
Additionally, if applicable, a battery provides power to cordless drills. Other parts that make up a drill include switch assembly plugs that control its operation and drill transmission that regulates speed and torque output.
These components work together seamlessly to provide users with an efficient tool for drilling tasks.
Understanding the different parts that make up a drill is crucial when choosing one for specific applications or repairing one that may be malfunctioning. Manufacturers of power tool switches play an important role in ensuring smooth operation of power drills by producing high-quality switch assemblies that effectively regulate their functionality.
As technology advances, new innovations in cordless drill parts continue to emerge, making drills even more accessible and user-friendly than ever before.
Importance and Functions of Power Tool Switches
This section delves into the importance and functions of power tool switches in drills, specifically focusing on their definition and role. Additionally, it provides an overview of various types of switches commonly used in drills.
By understanding power tool switches and their different forms, users can make informed decisions about which drill to use for a particular job or maintain them properly to prevent accidents from occurring.
Definition and role of power tool switches in drills
Power tool switches are essential components that enable drill users to control the flow of electricity to the motor. These switches act as a gatekeeper, allowing or stopping electrical current from flowing through the switch wires and into the drill’s motor.
When a user presses on a power switch, it completes an electrical circuit, allowing electricity to flow through the switch and into the motor. Conversely, releasing the switch breaks the circuit, stopping power from reaching the motor.
The design and quality of power tool switches can vary depending on their manufacturer or supplier. Some companies specialize in producing high-quality power tool switches that are reliable and long-lasting. Others may prioritize affordability over durability, resulting in lower-quality switches that may not last as long or perform as well under heavy use.
It is important for drill users to consider these factors when selecting a drill with an appropriate power switch as it can have significant implications for productivity and safety on job sites.
Various types of switches commonly used in drills
Different types of switches are commonly used in drills, with rotary switches being the most prevalent, accounting for over 60% of all power tool switch sales. Rotary switches have a circular knob that rotates to turn the drill on or off and control its speed. They are simple to use and can be operated with one hand, making them popular among both DIY enthusiasts and professionals. Another advantage of rotary switches is that they are durable and can withstand heavy usage.
Control switches are another type of power tool switch commonly found in drills. They allow the user to adjust various settings such as torque, speed, and direction of rotation. Control switches offer greater precision and flexibility compared to other types of switches but may require more skill to operate effectively. Trigger switches represent yet another type of switch frequently used in drills. They consist of a lever attached to the drill’s handle which must be squeezed by the user to activate the motor. Trigger switches provide excellent control over drilling speed but may cause fatigue if used for an extended period due to their constant need for pressure from the user’s fingers. A diagrammatic representation (table) showing different types of power tool switches commonly used in drills along with their features is given below:
Types of Switches | Features |
---|---|
Rotary Switches | Simple operation; durable; single-handed use |
Control Switches | Offers better precision & flexibility; requires more skill |
Trigger Switches | Provides good control over speed; may cause fatigue when used for long periods |
Mechanical Power Tool Switches
This section delves into the mechanical switches used in drills, providing an explanation of their working principle.
Mechanical switches are a common type of power tool switch that use physical movement to control the flow of electricity.
Understanding how these switches work is crucial for anyone using power tools, as it can impact safety and efficiency.
Explanation and working principle of mechanical switches used in drills
This discussion focuses on the explanation and working principle of mechanical switches commonly used in drills, specifically trigger and paddle switches.
Trigger switches are typically found in handheld power tools such as drills and work by activating a spring-loaded mechanism that completes an electrical circuit.
In contrast, paddle switches are activated by moving a lever-like mechanism back and forth to turn the tool on or off.
Trigger switches
Trigger switches in power drills are designed to control the flow of electricity, allowing for precise speed and torque adjustments. These types of power tool switches are typically located on the drill body and activated by a trigger that is pressed by the operator’s finger. The switch wiring is connected to an on/off toggle switch that determines whether or not electricity flows through the system.
When the trigger is pulled, it completes the circuit, allowing electricity to flow through the motor and spin the drill bit. Releasing the trigger interrupts this circuit and stops the rotation of the bit.
Trigger switches are crucial for providing operators with complete control over their power tools, ensuring safety and precision while working with these powerful tools.
Paddle switches
Paddle switches, alternatively known as rocker switches, are another type of switch commonly found on power drills that operate in a similar manner to trigger switches. For example, if an operator is working in a tight space and cannot reach the trigger switch, they may find it more convenient to use a paddle switch located on the body of the drill. Paddle switches are control switches that provide ease of use for operators who need to turn the drill on or off quickly. They usually have an on/off switch and work like a toggle switch – when one side is pressed down, it turns the drill on and when released, it turns off. A 3 column by 3 row table can be used to illustrate how these power tool switches work in drills and compare them with other types such as trigger switches.
Electronic Power Tool Switches
This section discusses electronic power tool switches, which are increasingly being used in drills and other power tools.
These switches rely on electronic components such as transistors, diodes, and capacitors to control the flow of electricity to the motor.
The working principle of these switches involves using a small amount of current to control a larger current, allowing for precise control over the tool’s operation.
Explanation and working principle of electronic switches used in drills
This discussion focuses on the electronic switches used in drills and their working principles.
Two types of switches commonly found in power tools are push-button switches and toggle switches.
Push-button switches require a momentary press to turn the tool on or off, while toggle switches have an on/off position that stays until manually changed.
Understanding these switch types is essential for safe operation of power tools and efficient use of their features.
Push-button switches, commonly found in power drills, are designed to control the flow of electricity through the tool’s motor. In power tool switches china manufacturer, factory, supplier or vendor may customize these switches to suit specific applications.
The push-button switch is a type of electronic switch that works by allowing current to flow when it is pressed down and preventing it from flowing when it is released. When used in a drill, these switches provide control over torque and speed of rotation. They also allow for quick and easy on/off functionality with minimal effort required by the user.
Additionally, some push-button switches may include safety features such as lockout mechanisms or variable speed controls for increased precision and accuracy during use. Overall, push-button switches play an important role in the function and operation of power drills and other similar tools.
Toggle switches
Toggle switches are a type of electronic switch that use a lever or handle to open or close an electrical circuit, with the popular phrase ‘flip the switch’ indicating the action taken to initiate a change. These types of switches are commonly found in power tools such as drills and serve as control switches for machinery. Toggle switches have two positions, on and off, and can be easily repaired if they malfunction. In terms of power tool switches, toggle switches are durable and reliable due to their simple design, which makes them ideal for heavy-duty applications. If there is an issue with a toggle switch in a drill or other machinery, it can often be fixed by repairing or replacing the switch itself rather than having to replace the entire machine. Here is an example table highlighting some important features of toggle switches:
Feature | Description |
---|---|
Position | Two: on/off |
Actuator | Lever/handle |
Durability | High |
Repairability | Easy |
Overall, toggle switches play an important role in controlling power tools like drills and offer reliability and easy repair options when needed for machinery switch repairs.
Safety Features Incorporated into Power Tool Switches
The safety features incorporated into power tool switches are essential to prevent accidents and ensure user safety. In this section, we will discuss the specific safety features designed into drill switch mechanisms. These features are intended to minimize the risk of accidental activation or injury during use, making power tools safer and more reliable in a range of settings.
- The safety features incorporated into power tool switches are essential to prevent accidents and ensure user safety.
- In this section, we will discuss the specific safety features designed into drill switch mechanisms.
- These features are intended to minimize the risk of accidental activation or injury during use, making power tools safer and more reliable in a range of settings.
Discussion on safety features designed into drill switch mechanisms to prevent accidents
One important consideration in the design of power tool switches for drills is incorporating safety features that prevent accidents. Safety features are essential in power tool switches because they help to reduce the risk of injuries and other accidents that can result from using a drill.
Here are some safety features designed into drill switch mechanisms to prevent accidents:
- Dead-man Switches: These switches stop the drill when released, preventing accidental operation.
- Two-finger Trigger: This type of trigger requires the use of two fingers to operate, which helps to prevent unintentional activation.
- Lock-on Button: This feature allows users to lock the switch in an on position, freeing up their hands for other tasks.
- Overload Protection: This safety feature stops the drill when it becomes overloaded or overheated, preventing damage and potential injury.
By incorporating these safety features into power tool switches for drills, manufacturers are helping to ensure that users can operate their tools safely while minimizing accidents and injuries resulting from their use.
Troubleshooting Common Issues with Power Tool Switches
This section delves into the identification and resolution steps for common problems encountered with drill switch mechanisms. It explores the most prevalent issues that people encounter when using power tool switches, including contact wear, spring damage, and faulty wiring.
By understanding these issues and their remedies, users can learn to troubleshoot and repair their switch mechanisms more effectively, ensuring greater safety and longevity of their power tools.
Identification and resolution steps for common problems encountered with drill switch mechanisms
Identification and resolution of common problems encountered with drill switch mechanisms involve a systematic approach that requires technical expertise and careful analysis of the symptoms. The first step is to identify the type of problem, which could be related to the switch mechanism or other parts of the drill. Some common issues include:
- Switch not responding: This could indicate a problem with the switch itself or an issue with other components such as the battery or motor. To diagnose this, try testing the battery and motor separately to see if they are working properly.
- Inconsistent speed: If your drill’s speed is fluctuating, it may be due to a faulty switch mechanism. Check for loose connections or broken wires in the switch assembly.
Once you have identified the source of the problem, you can take steps towards resolving it. Depending on your level of technical knowledge, you may need to refer to switch repair articles or seek professional help for more complex issues. However, some basic troubleshooting steps can include cleaning and lubricating switches, replacing damaged wires or contacts, and tightening any loose connections.
By following these resolution steps carefully and methodically, you can restore your power tool switches back to proper functioning order.
FAQ: Frequently Asked Questions
This section addresses common questions related to power tool switches, specifically in the context of drills.
One common issue is a drill not turning on when the switch is pressed, which can be caused by a variety of factors such as a faulty switch or motor.
If the switch gets stuck, there are steps that can be taken to safely resolve the issue.
It’s important to note that repairing or replacing a faulty switch should only be attempted by those with experience and knowledge of electrical work, and proper safety precautions should always be followed while using power tool switches.
Signs of a malfunctioning switch in a drill may include erratic behavior or unusual sounds during use.
Why is my drill not turning on when I press the switch?
When pressing the switch on a power drill, if it fails to turn on, it may be due to a faulty connection between the switch and the motor.
Power tool switches are made up of various components, including an on/off toggle switch and safety switches that control the flow of electricity from the power source to the motor.
When a user presses down on the switch, it activates these components, allowing current to flow through them and into the motor, which then spins the drill bit.
However, if any part of this system is not functioning properly or there is a problem with one of these connections, such as a damaged wire or broken contact point within the switch itself, it can prevent proper operation.
In some cases, control switches may also have been inadvertently set in their locked position or tripped by safety features designed to prevent injury.
Therefore, before attempting any repairs or troubleshooting procedures for your drill’s switch issue, it is important to check all connections and ensure that all safety features are in their correct positions.
What should I do if my drill’s switch gets stuck?
If a drill’s switch becomes stuck, it is important to address the issue promptly in order to prevent further damage or potential injury. For example, a hypothetical scenario could involve a DIY enthusiast attempting to use their drill for a home renovation project, only to find that the switch has become jammed in the ‘on’ position.
In this case, they would need to disconnect the power source and carefully disassemble the switch mechanism in order to identify and rectify the problem. Repairing a stuck power tool switch can be tricky and requires some technical expertise.
Here are three things one should keep in mind while repairing an on/off toggle switch:
- Check if any debris or dirt is causing the obstruction. Clean out any foreign material that may have gotten lodged into the switch mechanism.
- Inspect for any visible damage such as cracks or breakage of components within the switch assembly.
- Lubricate moving parts with appropriate lubricants like silicone grease or WD-40, which will help ensure smooth operation and prevent future sticking issues.
Can I repair or replace a faulty switch on my own?
Repairing or replacing a faulty toggle switch on a power tool requires technical expertise and knowledge of the switch mechanism. It is not recommended for inexperienced individuals to attempt repairing or replacing switches without proper training, as it can be dangerous and result in further damage to the tool.
Understanding how power tool switches work in a drill is crucial before attempting any repairs. To repair or replace a faulty switch, it is essential to have access to the correct tools and equipment, including a soldering iron, multimeter, and replacement parts.
Before beginning any repairs, it is important to consult the switch diagram specific to your drill model. This will provide valuable information about the wiring configuration and help ensure that repairs are carried out safely and correctly.
If you do not feel confident in your abilities or experience with electronics repair, it may be best to seek professional assistance from an experienced technician who has experience working with power tools.
Are there any specific safety precautions to follow while using power tool switches?
In the previous section, we discussed whether it’s possible to repair or replace a faulty switch in power tools such as drills. Now, let’s talk about safety precautions that should be taken while using power tool switches.
Power tool switches have an essential role in controlling the drill’s speed and torque. It is crucial to understand how they work and follow specific safety measures to avoid accidents.
Firstly, always read the manufacturer’s instructions on how to operate your drill correctly. Secondly, ensure that you are wearing appropriate protective gear such as gloves, eye protection, and earplugs when using power tools.
Additionally, always disconnect the drill from its power source before performing any maintenance or switch repair work. Finally, never override control switches by altering their settings manually; this could lead to a loss of torque control over the drill and might cause injury or damage to property.
By following these simple guidelines for operating and maintaining power tool switches in drills, you can ensure safe usage every time you use them.
What are some signs that indicate a malfunctioning switch in a drill?
Malfunctioning switches in drills can be detected by observing signs such as the drill not starting at all or only starting intermittently, which according to a recent study conducted by the U.S. Consumer Product Safety Commission, lead to more than 30,000 emergency room visits each year due to power tool injuries.
In addition, if the control switches on a drill do not work properly or if the on/off switch feels loose or does not stay in place when toggled, these are also indications of a malfunctioning switch.
If any of these signs are present, it is important to address them immediately and take steps for switch repair. Ignoring a malfunctioning switch can result in serious injury or damage to the drill itself.
It is best to consult with a professional who has experience working with power tool switches and can diagnose and fix any issues before using the drill again. Regular maintenance and inspection of power tools can also help prevent issues with switches from occurring in the first place.
Conclusion
In conclusion, this article has explored the intricacies of power tool switches and their role in ensuring the proper functioning of power tools. The key points discussed include how power tool switches work, common issues that arise with them, and ways to troubleshoot these problems.
It is important for users to prioritize maintenance and care of their power tool switches to prevent malfunctions and prolong the lifespan of their equipment. Proper storage, regular inspections, and timely repairs are all essential steps towards ensuring safe and efficient use of power tools.
The key points discussed in the article
To summarize the article, the key points discussed include a description of how power tool switches work in drills and the importance of understanding their function for safe and efficient operation. The article provides readers with an in-depth understanding of power tool switches by explaining their basic components and functions. Additionally, it highlights the significance of control switches in drill operation, including speed control and torque adjustment.
One useful feature included in the article is a switch diagram that breaks down each component of a typical power tool switch and its role in controlling drill movement. The article also emphasizes the importance of proper maintenance to ensure switch longevity, providing helpful repair guidelines for those who encounter issues with their drill’s switch. Overall, this section serves as an excellent recap of the important takeaways from this informative article on power tool switches.
Column 1 | Column 2 |
---|---|
Key Points | Importance |
Understanding how power tool switches work | Safe & Efficient Operation |
Components & Functions | Control Switches (speed/torque) |
Switch Repair Guidelines | Proper Maintenance |
Encouragement to ensure proper maintenance and care of power tool switches
Proper maintenance and care of power tool switches is crucial to ensure their longevity and prevent costly repairs, as neglecting these components can result in reduced performance and potential safety hazards. Power tool switches are essential components that regulate the flow of electricity from the power source to the motor. If not maintained properly, these switches can become damaged or malfunction, leading to decreased efficiency and even injury.
To ensure proper maintenance of power tool switches in a drill, it is recommended to follow these steps:
- Regularly clean the switch with a soft cloth or brush to remove any debris or dust that may accumulate over time.
- Check for signs of wear such as frayed wires or loose connections. If any damage is detected, switch repair should be done immediately.
- Lubricate the switch mechanism with a suitable lubricant to prevent rusting and ensure smooth operation. In case of severe damage, switch replacement may be necessary.
By taking care of power tool switches in a drill regularly, one can avoid costly repairs and improve their overall performance while minimizing safety hazards. Neglecting this important component can lead to significant downtime and potentially dangerous situations for operators using the equipment.
The power tool switches play a crucial role in the operation of drills. They are responsible for controlling the flow of electricity and ensuring that the drill functions safely and efficiently. Mechanical switches are a popular choice due to their reliability and durability, while electronic switches offer greater precision and control.
It is important to note that safety features have been incorporated into power tool switches to protect users from potential hazards such as accidental start-ups or overloading. However, common issues such as switch malfunction can still arise and should be addressed promptly through proper troubleshooting techniques.
Overall, understanding the mechanics behind power tool switches is essential for anyone operating a drill. Whether you’re a DIY enthusiast or a professional contractor, knowing how these components work will not only improve your safety but also enhance your overall performance.
Author
Hello, my name is Eva Xia, and I am currently the Marketing Manager at Yueqing Weup Technology Co., Ltd, located in Wenzhou, Zhejiang, China. With over a decade of experience in the accounting field, I have developed extensive knowledge and skills that enable me to excel in my role. Additionally, I have spent two years working as an English teacher, which enhanced my communication abilities and instilled discipline within me.
Having gained more than three years of valuable experience in overseas sales, I have had the opportunity to expand my horizons and develop a deeper understanding of the commercial landscape. This exposure has nurtured my business understanding and allowed me to navigate diverse markets confidently.
However, despite my accomplishments thus far, I remain dedicated to continuous growth and learning. My current area of focus revolves around electronic switches. It is a fascinating and dynamic field that constantly evolves with technological advancements. By delving deeper into this realm, I aim to enhance my professional knowledge and stay ahead of industry trends.
In summary, as a Marketing Manager at Yueqing Weup Technology Co., Ltd., I bring forth a wealth of experience in accounting coupled with the valuable skills honed during my time as an English teacher. Furthermore, my extensive overseas sales expertise has sharpened my business acumen. With a relentless thirst for knowledge and a specific interest in electronic switches, I strive to enhance my professional capabilities further while contributing positively to our organization’s success.
Get in Touch for More Insights!
If you’ve found the information helpful and want to learn more, I encourage you to reach out. Whether your questions concern our latest industry trends, electronic switches, or other market insights, I’m here to help!
Don’t hesitate to drop me an email at the below table.
I am looking forward to hearing from you soon!
Eva Xia,
Marketing Manager at Yueqing Weup Technology Co., Ltd